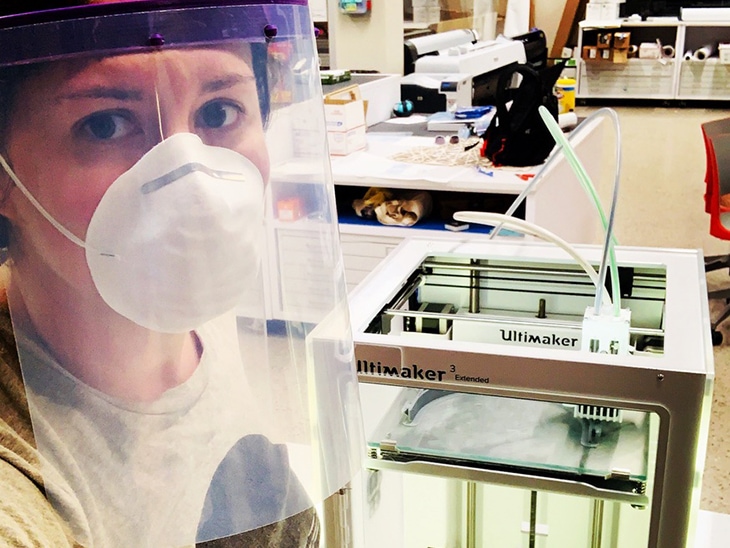
A University of Tampa instructor is using technology on the school’s campus to fabricate face shields to protect health care workers as they treat potential COVID-19 patients.
Emma Quintana, coordinator of UT’s Fab Lab, a workshop with a load of tech equipments for art students, is using the facilities eight 3D printers to make the shields.
Quintana designed the shields to cover users’ entire faces from glasses to below their chin. The shields still require use of an N95 mask for optimal protection, but add another layer of safety by protecting health care workers from droplets emitted through things like sneezing and coughing, which health officials say are how the virus spreads.
“It’s an amazing feat we are accomplishing, and it gives many of us a way to give back to our real heroes, medical workers,” Quintana said. “The idea that we don’t have to wait for factories abroad to deliver these life-saving objects is pretty incredible.”
Quintana uses the laser printers to develop the shield’s frame and a laser cutter to cut the clear plastic shield. Elastic is added to the back to secure the shield on the head.
Quintana will donate 100 face shields to Johns Hopkins All Children’s Hospital in St. Petersburg on Friday. A COVID-19 testing site in Tampa has also expressed interest in obtaining some of the shields, according to UT.
From start to finish, it takes Quintana about six hours to complete one face shield. She’s been working on the project since mid-March when UT, and colleges and universities across the state, began shifting to remote learning.
Quintana is working on the project in the lab alone, so she’s more than abiding by Centers for Disease Control and Prevention social distancing guidelines, but she has had inspiration from others in the Fab Lab global community.
“There is a thriving open-source 3D printing community, and many makers around the country are working to address the PPE (personal protective equipment) shortages within their local communities,” Quintana said. “These recent shortages and the role local makers are taking by becoming small-scale manufacturers show the flexibility of these spaces and the ingenuity of the making community: arts and engineers working together.”